Gli stabilimenti tedeschi iniziano a realizzare pezzi centrali per l’autocarro Mercedes eActros. Ciò include l’asse elettrico e i pacchi batteria, che vengono prodotti e assemblati nelle sedi di Gaggenau, Kassel e Mannheim. I componenti verranno quindi utilizzati nella versione in serie, che vedrà la luce dal 7 ottobre 2021 presso l’impianto di Wörth.
Mercedes eActros: i pacchi batteria di Mannheim
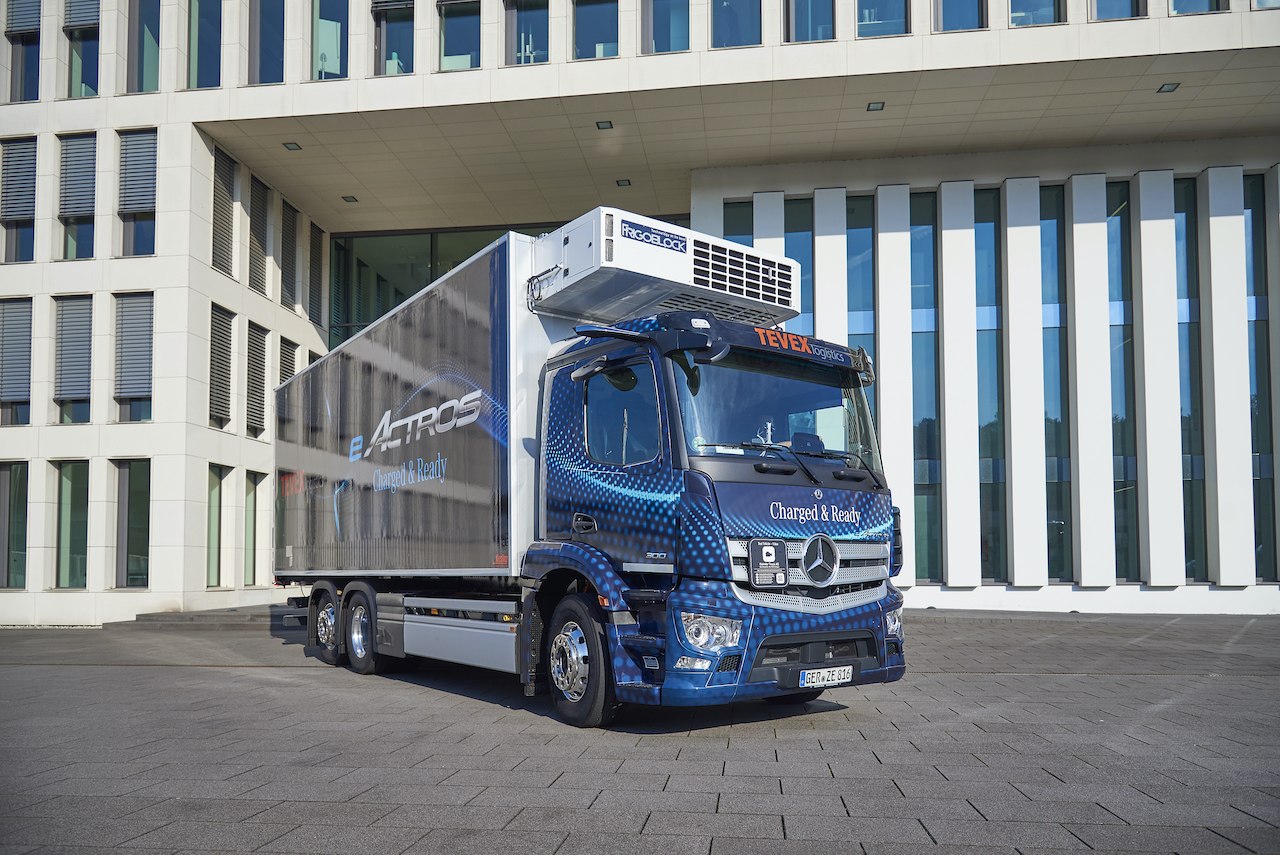
Nel Competence Center for Emission-Free Mobility (KEM) di Mannheim, i moduli vengono sottoposti a un test funzionale. Un pacco batteria è composto da sei unità singole. Il pacchetto è complessivamente lungo quasi 2,20 metri, largo 75 cm e alto 55 cm. Ma prima di renderlo pronto all’uso, i singoli moduli vengono inseriti in un alloggiamento di metallo e quindi collegati ad altre parti come sbarre, unità di controllo e cavi.
Seguono il cablaggio e l’applicazione di strati isolanti che garantiscono i più elevati standard di sicurezza. Infine, il cosiddetto E/E box è fissato all’alloggiamento metallico premontato, che in seguito costituisce l’interfaccia tra la batteria e il veicolo. Anche la scatola E/E è preassemblata a Mannheim. Dopo gli ultimi preparativi e un test di tenuta, viene inviato al centroBenz di Wörth.
L’asse elettronico: un ruolo chiave per la fabbrica di Kassel
Gli operai di Kassel compongono l’intero asse elettrico, costituito da ponte assale, propulsore elettrico ed elementi di trasmissione commutabili. Innanzitutto, i mozzi delle ruote e i dischi dei freni vengono allestiti. Allo stesso tempo, l’unità di trasmissione che include il cambio a due velocità è premontata. Le parti della trasmissione necessarie sono fornite dalla fabbrica di Gaggenau. Prima che l’asse elettrico sia preparato per la spedizione, viene eseguito un test funzionale e ad alta tensione. In particolare, nel corso di tali procedure vengono verificati i livelli di protezione e rumore.
L’e-axle è costruito sulla stessa base della corrispondente serie convenzionale. Pertanto, è possibile integrare sia i processi di fabbricazione che di installazione dell’e-axle su basi preesistenti. Questo comporta dei notevoli vantaggi in termini di flessibilità ed accessibilità.
Componenti rilevanti per la trasmissione per l’asse elettrico a Gaggenau
Nell’impianto di Gaggenau vengono adottate le tecniche più evolute per la produzione di parti meccaniche rilevanti per il cambio e i relativi alloggiamenti. Una sfida difficile, da affrontare con la massima precisione. Ciò è essenziale per assicurare una perfetta funzionalità e un comportamento acustico ottimale dell’asse elettrico. La gamma del centro di Gaggenau spazia dal più piccolo ingranaggio con un diametro esterno di 57 mm a quello di uscita con un diametro esterno di 365 mm e un peso grezzo di oltre 40 kg. Un totale di dieci elementi di trasmissione e tre di alloggiamento saranno consegnate a Kassel, dove avranno luogo i lavori conclusivi dell’e-axle.
Yaris Pürsün, Head of Global Production of Drive Components per Daimler Truck, ha sottolineato quanto il via libera significhi molto per loro. Si stanno prodigando affinché Mercedes eActros abbia qualità e non disperda anidride carbonica nell’ambiente. Pürsün ne ha approfittato per rimarcare, poi, i severi standard osservati. Gli sforzi segnano l’inizio di una nuova era per la rete produttiva e tecnologica in Germania.